Magnetic-Abrasive Surface Treatment: Polishing, Conditioning, Modification
The innovation and its applications
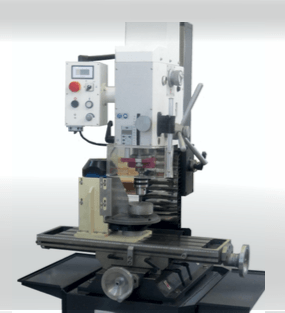
The product of this innovation is a sample of the multipurpose equipment called M14, which will provide the finishing technology of the Magnetic-Abrasive Machining of surfaces of machines' and devices' components.
The M14 unit is implemented on the basis of multipurpose drilling and milling machine, additionally equipped with a number of special units including two replaceable assemblies to perform the following:
- flat surfaces polishing to ensure the minimum roughness
- conditioning the edges of plates and cowls before welding
- polishing the rotation body surfaces in order to ensure the minimum roughness
- surface modification to improve the critical performance properties: resistance to corrosion, wear and mechanical failure
Problem relevance and industry state of art
The dynamics of machine-building and instrument-making industries is associated with the advanced implementation of products from hard-treated metals and their alloys. A complicated task is their finishing polishing and surface conditioning before the coating application and welding. These operations are generally perfomed by the mechanical methods, chemical etching or electrochemical polishing. These technologies are labor-intensive and environmentally unfriendly, poorly mechanized and automated, and they not always meet modern production requirements.
The proper metalware welding is possible only after a careful welded surface conditioning (cleaning) from oxide films, defects and impurities. Otherwise, they get into the welding seam and reduce its strength and corrosion resistance. The surfaces of articles made from reactive alloys based on aluminum, magnesium and titanium are particularly difficult to prepare for welding.
The traditional surface preparation for welding involves its mechanical conditioning (sandpaper, scraper or with metal wire brushes) or chemical treatment. However, the mentioned methods have several disadvantages, the main of which are low productivity, environmental inferiority and creation of an electrochemically active surface prone to rapid recreation of the removed oxide film.
Innovative technology – Magnetic-Abrasive Machining (MAM)
MAM method. Description, features and benefits
The MAM method is performed by ferro-abrasive powder tool that is compressed under the magnetic field influence, pressed against the treated surface and polishes it.
In contrast to the traditional abrasive technologies, during MAM prevail the processes of sub-microabrasion, elasto-plastic metal shift and surface microsmoothing. The temperature in the contact zone of ferro-abrasive grain and the workpiece is less than 150°C, which prevents the formation of the surface defects usual for abrasion. The applied pulsing magnetic field is very important at MAM. It facilitates the action of magnetoplastic, magnetoelectric and magnetostrictive defects in the workpiece surface layer. Under their influence, the weakly-fixed structural defects (dislocations, disclinations, rotations, etc.), formed during previous treatment operations, are set in motion (like Brownian). A significant part of the moving defects comes to the surface and the "soft brush" of ferro-abrasive powder forms surface nanorelief with minimal roughness and surface layer with a minimum of structural defects – potential sources of material failure.
The MAM method surpasses the known analogues in technological opportunities, economic and environmental friendliness.
Magnetic-Abrasive Polishing (MAP)
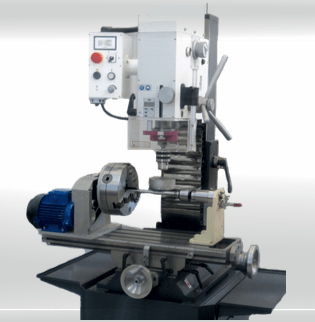
For MAP of the flat plates with a diameter of 15-200 mm and a thickness of up to 12 mm, in order to reduce the surface roughness, the advanced development sample of multipurpose unit M14 is equipped with the assembly containing rotary drive and polished details fastening mechanism. The M14 provides simultaneous polishing of 4-24 details with a diameter of 15-80 mm. For example, the MAP of fluoride single-crystal plates (CaF2, MgF2, BaF2) with a diameter of 26 mm in 5-15 minutes provides the decrease in surface roughness by 10-20 times (from Ra=20 nm to Ra=1...2 nm) and the improvement in characteristics macrogeometry by 10-30%.
Magnetic-Abrasive Conditioning (MAC)
For space and aircraft industry, POLIMAG solved a difficult problem of conditioning the edges of the aircraft structural elements – cowls and plates from Al-Mg alloys. The oxide films and impurities are removed from the edges surfaces under MAM optimal mode. The thin glassy oxide film is formed. It does not essentially spread; it protects the base metal from corrosion. During welding, 100% of the film is decomposed under the influence of flux and welding arc; it does not deposit defects into the formed welding seam. The edges weldability after MAC is at least 30 days, while for the alternative operations (chemical etching and mechanical scraping) these characteristics are 33% and two days respectively.
The welding seam tests on mechanical strength (tensile strength, yield strength and others) showed that the edges conditioning in the magnetic field provides higher values of these characteristics than the samples after electro-chemical polishing and chemical etching. As MAC does not require toxic acid and alkali solutions, this technology is better from ecological and economic points of view.
Good results are obtained after MAC application for conditioning of the surfaces of alloyed (stainless) steel sheet - for example products before their thermodiffusion welding. The MAC technology application is effective in various technical fields.
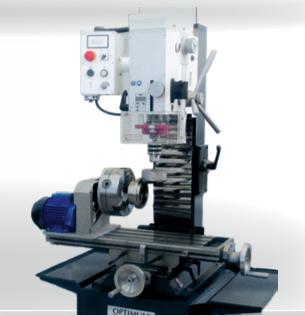
The M14 unit with the corresponding setup provides conditioning the edges of the plates up to 12 mm in thickness and cowls with 300 mm in diameter and 10 mm in wall thickness. The MAC operation performance is up to 2.5 m/min. The M14 unit provides polishing of the rotation body surfaces with diameter up to 200 mm.
Magnetic-Abrasive Surface Modification (MASM)
Magnetic-abrasive machining significantly reduces surface micro- and nanorelief and provides essential surface layer modification. It allows:
- to improve the structure and surface layer condition under the magnetic field influence in order to ensure high values of the most important operational properties – resistance to corrosion, abrasion and mechanical damage;
- to saturate the surface layer with alloying elements – iron, nickel, etc..